ແຜ່ນຕັດມີພາລະບົດບາດສໍາຄັນໃນອຸດສາຫະກໍາຕ່າງໆ, ອໍານວຍຄວາມສະດວກໃນຮູບຮ່າງແລະສໍາເລັດຮູບຂອງວັດສະດຸ. ຢ່າງໃດກໍຕາມ, ເຊັ່ນດຽວກັນກັບເຄື່ອງມືອື່ນໆ, ພວກເຂົາເຈົ້າບໍ່ມີພູມຕ້ານທານກັບບັນຫາທີ່ສາມາດຂັດຂວາງປະສິດທິພາບແລະປະສິດທິພາບຂອງເຂົາເຈົ້າ. ໃນບົດຄວາມນີ້, ພວກເຮົາຈະເຈາະເລິກບັນຫາທົ່ວໄປຂອງແຜ່ນ grinding, ຄົ້ນຫາສາເຫດຮາກຂອງເຂົາເຈົ້າ, ແລະສະຫນອງການແກ້ໄຂປະສິດທິພາບສໍາລັບການເຮັດວຽກທີ່ບໍ່ມີ seamless.
ແນະນຳ
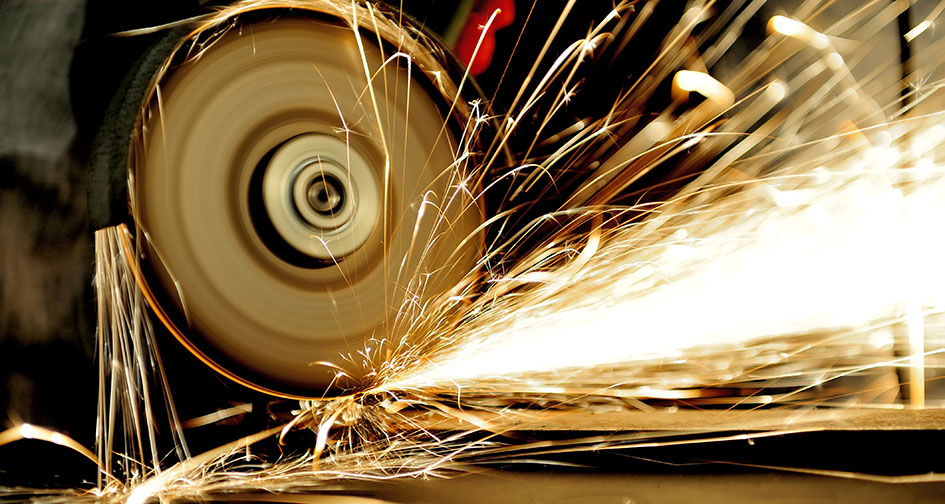
ແຜ່ນ Grinding ມີບົດບາດພື້ນຖານໃນອຸດສາຫະກໍາຕ່າງໆ, ເປັນເຄື່ອງມືທີ່ຈໍາເປັນສໍາລັບການໂຍກຍ້າຍວັດສະດຸ, ຮູບຮ່າງ, ແລະຂະບວນການສໍາເລັດຮູບ. ການເຂົ້າໃຈຄໍານິຍາມຂອງພວກເຂົາ, ຄວາມສໍາຄັນໃນທົ່ວອຸດສາຫະກໍາ, ແລະບັນຫາທົ່ວໄປທີ່ປະເຊີນຫນ້າແມ່ນສໍາຄັນສໍາລັບການເພີ່ມປະສິດທິພາບການນໍາໃຊ້ຂອງພວກເຂົາແລະຮັບປະກັນການປະຕິບັດງານທີ່ມີປະສິດທິພາບ.
A. ຄໍານິຍາມຂອງແຜ່ນຕັດ
ແຜ່ນຂັດແມ່ນເຄື່ອງມືຂັດທີ່ຖືກນໍາໃຊ້ໃນຂະບວນການເຄື່ອງຈັກເພື່ອຕັດ, ຂັດ, ຫຼືຂັດພື້ນຜິວຂອງວັດສະດຸ. ແຜ່ນເຫຼົ່ານີ້ປົກກະຕິແລ້ວປະກອບດ້ວຍອະນຸພາກຂັດທີ່ຜູກມັດກັບວັດສະດຸຮອງ, ສ້າງເຄື່ອງມືຫມຸນທີ່ສາມາດເອົາວັດສະດຸເກີນ, ດ້ານກ້ຽງ, ຫຼືແຫຼມ. ພວກເຂົາມາໃນຮູບຮ່າງແລະຂະຫນາດຕ່າງໆ, ແຕ່ລະຄົນຖືກອອກແບບມາສໍາລັບຄໍາຮ້ອງສະຫມັກສະເພາະ.
B. ຄວາມສໍາຄັນໃນອຸດສາຫະກໍາຕ່າງໆ
ອຸດສາຫະກໍາໂລຫະ:
ໃນການຜະລິດແລະການຜະລິດໂລຫະ, ແຜ່ນບົດແມ່ນສໍາຄັນສໍາລັບການສ້າງຮູບຊົງ, ການຂັດຂີ້ເຫຍື້ອ, ແລະສໍາເລັດຮູບດ້ານໂລຫະ. ພວກມັນຖືກນໍາໃຊ້ທົ່ວໄປກັບເຄື່ອງຕັດມຸມເພື່ອບັນລຸຂະຫນາດທີ່ຊັດເຈນແລະຄຸນນະພາບຂອງຫນ້າດິນ.
ອຸດສາຫະກໍາການກໍ່ສ້າງ:
ຜູ້ຊ່ຽວຊານດ້ານການກໍ່ສ້າງແມ່ນອີງໃສ່ແຜ່ນ grinding ສໍາລັບວຽກງານເຊັ່ນ: ການກະກຽມດ້ານສີມັງ, ກ້ຽງຂອບ rough, ແລະກໍາຈັດຄວາມບໍ່ສົມບູນຂອງວັດສະດຸເຊັ່ນ: ແກນແລະຊີມັງ.
ອຸດສາຫະກຳລົດຍົນ:
ແຜ່ນຂັດແມ່ນມີຄວາມຈໍາເປັນໃນຂະແຫນງການລົດຍົນສໍາລັບວຽກງານຕ່າງໆຕັ້ງແຕ່ເຄື່ອງມື sharpening ກັບຮູບຮ່າງແລະສໍາເລັດຮູບອົງປະກອບໂລຫະ. ພວກເຂົາເຈົ້າປະກອບສ່ວນກັບຄວາມແມ່ນຍໍາແລະຄຸນນະພາບຂອງພາກສ່ວນລົດຍົນ.
ອຸດສາຫະກໍາໄມ້:
ຊ່າງໄມ້ໃຊ້ແຜ່ນບົດເພື່ອເຮັດຮູບຮ່າງ ແລະເຮັດໃຫ້ພື້ນຜິວຂອງໄມ້ລຽບ. ແຜ່ນເຫຼົ່ານີ້ມີປະສິດຕິຜົນໃນການເອົາວັດສະດຸທີ່ເກີນ, ປັບປຸງຮູບຮ່າງ, ແລະກະກຽມໄມ້ສໍາລັບການສໍາເລັດຮູບຕື່ມອີກ.
ການຜະລິດທົ່ວໄປ:
ແຜ່ນ grinding ຄົ້ນຫາຄໍາຮ້ອງສະຫມັກໃນຂະບວນການຜະລິດຕ່າງໆທີ່ຕ້ອງການການໂຍກຍ້າຍວັດສະດຸທີ່ຊັດເຈນ, ປະກອບສ່ວນເຂົ້າໃນການຜະລິດອົງປະກອບທີ່ມີຄຸນນະພາບສູງ.
C. ບັນຫາທົ່ວໄປທີ່ປະເຊີນ
ການສວມໃສ່ແຜ່ນດິດ ແລະການຂັດ:
ການນໍາໃຊ້ຢ່າງຕໍ່ເນື່ອງສາມາດນໍາໄປສູ່ການສວມໃສ່ແລະການຂັດຂອງແຜ່ນ grinding, ຜົນກະທົບຕໍ່ການປະຕິບັດຂອງມັນ. ການກວດກາປົກກະຕິແລະການທົດແທນແມ່ນມີຄວາມຈໍາເປັນເພື່ອຮັກສາປະສິດທິພາບ.
ຄວາມຮ້ອນເກີນ:
friction ຫຼາຍເກີນໄປໃນລະຫວ່າງການນໍາໃຊ້ເປັນເວລາດົນນານອາດຈະນໍາໄປສູ່ການ overheating, ຜົນກະທົບຕໍ່ຄວາມທົນທານຂອງແຜ່ນແລະຄຸນນະພາບຂອງຫນ້າດິນສໍາເລັດຮູບ. ມາດຕະການຄວາມເຢັນທີ່ເຫມາະສົມແລະການພັກຜ່ອນແຕ່ລະໄລຍະແມ່ນຈໍາເປັນ.
ການອຸດຕັນ:
ແຜ່ນບົດສາມາດສະສົມສິ່ງເສດເຫຼືອຂອງວັດສະດຸ, ຫຼຸດຜ່ອນປະສິດທິພາບຂອງມັນ. ການທໍາຄວາມສະອາດເປັນປົກກະຕິຫຼືເລືອກແຜ່ນທີ່ມີລັກສະນະຕ້ານການອຸດຕັນຊ່ວຍປ້ອງກັນບັນຫານີ້.
ການສັ່ນສະເທືອນ ແລະ ການສັ່ນສະເທືອນ:
ຄວາມບໍ່ສົມດຸນຫຼືການສວມໃສ່ບໍ່ສະຫມໍ່າສະເຫມີອາດຈະເຮັດໃຫ້ເກີດການສັ່ນສະເທືອນຫຼືການສັ່ນສະເທືອນ, ຜົນກະທົບຕໍ່ຄຸນນະພາບຂອງການສໍາເລັດຮູບແລະຄວາມປອດໄພຂອງການດໍາເນີນງານ. ການຕິດຕັ້ງແລະການດຸ່ນດ່ຽງທີ່ເຫມາະສົມແມ່ນສໍາຄັນ.
ການເລືອກແຜ່ນບໍ່ຖືກຕ້ອງ:
ການເລືອກແຜ່ນຂັດຜິດປະເພດສໍາລັບອຸປະກອນການສະເພາະໃດຫນຶ່ງຫຼືຄໍາຮ້ອງສະຫມັກສາມາດນໍາໄປສູ່ການບໍ່ມີປະສິດທິພາບແລະຄວາມເສຍຫາຍທີ່ອາດມີ. ການເລືອກທີ່ເຫມາະສົມໂດຍອີງໃສ່ຄວາມເຂົ້າກັນໄດ້ຂອງວັດສະດຸແມ່ນເປັນສິ່ງຈໍາເປັນ.
ຄວາມເຂົ້າໃຈກ່ຽວກັບຄໍານິຍາມ, ຄວາມສໍາຄັນ, ແລະສິ່ງທ້າທາຍທີ່ເປັນໄປໄດ້ທີ່ກ່ຽວຂ້ອງກັບແຜ່ນ grinding ເປັນສິ່ງຈໍາເປັນສໍາລັບອຸດສາຫະກໍາທີ່ອີງໃສ່ເຄື່ອງມືເຫຼົ່ານີ້. ໂດຍການແກ້ໄຂບັນຫາທົ່ວໄປແລະການຮັບປະກັນການນໍາໃຊ້ທີ່ເຫມາະສົມ, ອຸດສາຫະກໍາສາມາດເພີ່ມປະສິດທິພາບສູງສຸດຂອງການຂັດແຜ່ນໃນຄໍາຮ້ອງສະຫມັກຂອງພວກເຂົາ.
ສວມໃສ່ ແລະ ຈີກຂາດໃນແຜ່ນຂັດ
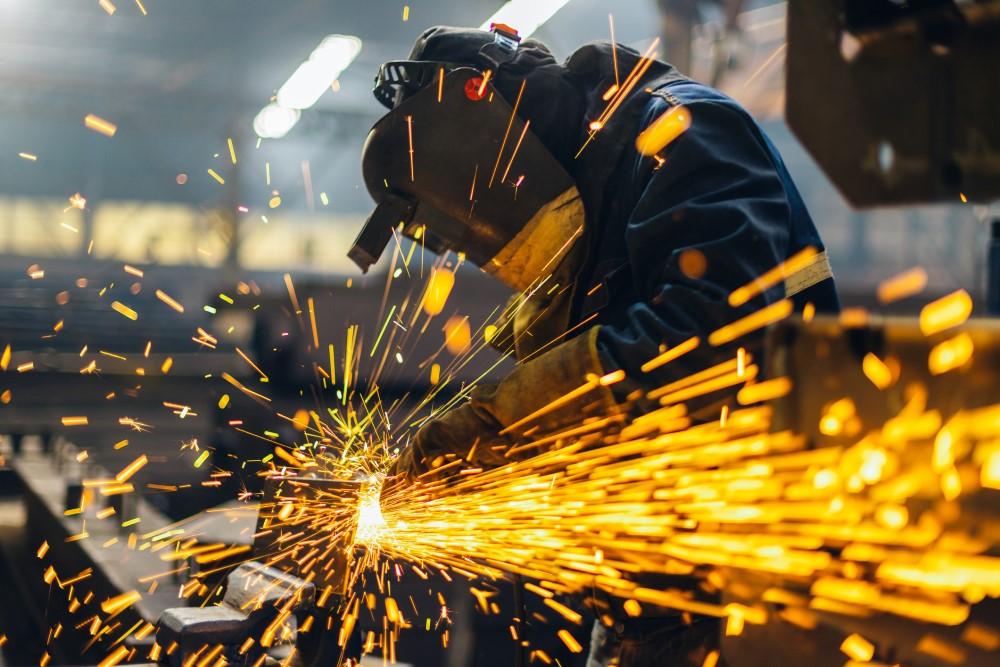
ແຜ່ນຂັດແມ່ນເຄື່ອງມືທີ່ຈໍາເປັນໃນອຸດສາຫະກໍາຕ່າງໆ, ສະຫນອງການຂັດທີ່ຈໍາເປັນສໍາລັບວຽກງານຕ່າງໆຕັ້ງແຕ່ການຜະລິດໂລຫະຈົນເຖິງການຂັດສີມັງ. ຄວາມເຂົ້າໃຈກ່ຽວກັບປັດໃຈທີ່ເຮັດໃຫ້ເກີດການສວມໃສ່ ແລະຈີກຂາດຂອງແຜ່ນຂັດແມ່ນສໍາຄັນສໍາລັບການເພີ່ມປະສິດທິພາບຂອງພວກມັນ ແລະຮັບປະກັນຄວາມປອດໄພ.
ຄວາມແຂງຂອງວັດສະດຸແລະອົງປະກອບ:
ການປ່ຽນແປງຄວາມແຂງ:ແຜ່ນຂັດຈະພົບກັບວັດສະດຸທີ່ມີລະດັບຄວາມແຂງແຕກຕ່າງກັນ. ວັດສະດຸຂັດເຊັ່ນໂລຫະແລະສີມັງສາມາດແຕກຕ່າງກັນຢ່າງຫຼວງຫຼາຍໃນຄວາມແຂງ. ການຂັດຢ່າງຕໍ່ເນື່ອງຕໍ່ກັບວັດສະດຸແຂງເລັ່ງການສວມໃສ່.
ອົງປະກອບຂອງວັດສະດຸ:ການປະກົດຕົວຂອງອົງປະກອບຂັດຢູ່ໃນວັດສະດຸທີ່ເປັນພື້ນດິນສາມາດສົ່ງຜົນກະທົບຕໍ່ການສວມໃສ່ໃນແຜ່ນການຂັດ. ອະນຸພາກຂັດສາມາດເລັ່ງການສວມໃສ່ຂອງແຜ່ນ.
ຄວາມດັນ ແລະແຮງບີບອັດ:
ຄວາມກົດດັນຫຼາຍເກີນໄປ:ການໃຊ້ແຮງດັນຫຼາຍເກີນໄປໃສ່ແຜ່ນຂັດສາມາດນໍາໄປສູ່ການສວມໃສ່ໄວ. ມັນເປັນສິ່ງຈໍາເປັນທີ່ຈະໃຊ້ຄວາມກົດດັນທີ່ແນະນໍາສໍາລັບຄໍາຮ້ອງສະຫມັກສະເພາະເພື່ອຫຼີກເວັ້ນການເມື່ອຍທີ່ບໍ່ຈໍາເປັນໃນແຜ່ນ.
ກໍາລັງບໍ່ພຽງພໍ: ໃນອີກດ້ານຫນຶ່ງ, ກໍາລັງບໍ່ພຽງພໍອາດຈະເຮັດໃຫ້ການ grinding ຍາວ, ການສ້າງ friction ແລະຄວາມຮ້ອນເພີ່ມເຕີມ, ປະກອບສ່ວນກັບການສວມໃສ່.
ຄຸນນະພາບແລະການປະກອບແຜ່ນ:
ຄຸນະພາບຂອງວັດສະດຸຂັດ:ຄຸນນະພາບຂອງວັດສະດຸຂັດທີ່ນໍາໃຊ້ໃນແຜ່ນ grinding ມີອິດທິພົນຕໍ່ຊີວິດຂອງມັນຢ່າງຫຼວງຫຼາຍ. ວັດສະດຸຂັດທີ່ມີຄຸນນະພາບສູງມີແນວໂນ້ມທີ່ຈະຕ້ານການສວມໃສ່ແລະຮັກສາຄວາມຄົມຊັດໄດ້ດົນກວ່າ.
ຕົວແທນພັນທະບັດ:ຕົວແທນການຜູກມັດທີ່ຖືອະນຸພາກ abrasive ຮ່ວມກັນມີບົດບາດສໍາຄັນ. ຕົວແທນການຜູກມັດທີ່ຖືກອອກແບບຢ່າງດີຊ່ວຍເພີ່ມຄວາມທົນທານຂອງແຜ່ນ.
ເງື່ອນໄຂສະພາບແວດລ້ອມບ່ອນເຮັດວຽກ:
ອຸນຫະພູມ:ອຸນຫະພູມສູງທີ່ສ້າງຂຶ້ນໃນລະຫວ່າງການຜະລິດສາມາດສົ່ງຜົນກະທົບອົງປະກອບຂອງແຜ່ນໄດ້. ຄວາມຮ້ອນຫຼາຍເກີນໄປເຮັດໃຫ້ສານຜູກມັດອ່ອນລົງແລະເລັ່ງການສວມໃສ່.
ຄວາມຊຸ່ມຊື່ນ ແລະສິ່ງປົນເປື້ອນ:ການສໍາຜັດກັບຄວາມຊຸ່ມຊື່ນຫຼືສິ່ງປົນເປື້ອນໃນສະພາບແວດລ້ອມບ່ອນເຮັດວຽກສາມາດສົ່ງຜົນກະທົບຕໍ່ຄວາມສົມບູນຂອງແຜ່ນຂັດ, ເຮັດໃຫ້ການສວມໃສ່ໄວຂຶ້ນ.
ເຕັກນິກການປະຕິບັດການ:
ເຕັກນິກທີ່ເຫມາະສົມ:ທັກສະຂອງຜູ້ປະຕິບັດງານແລະເຕັກນິກແມ່ນສໍາຄັນ. ການນໍາໃຊ້ທີ່ບໍ່ເຫມາະສົມ, ເຊັ່ນ: ການຂັດຢູ່ໃນມຸມທີ່ບໍ່ຖືກຕ້ອງຫຼືການໃຊ້ແຮງຫຼາຍເກີນໄປ, ສາມາດເຮັດໃຫ້ການສວມໃສ່ທີ່ບໍ່ສະເຫມີກັນແລະຫຼຸດຜ່ອນອາຍຸຂອງແຜ່ນ.
ການກວດກາປົກກະຕິ:ຜູ້ປະຕິບັດການຄວນກວດກາແຜ່ນຂັດເປັນປະຈໍາສໍາລັບອາການຂອງຄວາມເສຍຫາຍຫຼືການສວມໃສ່. ແຜ່ນທີ່ສະແດງໃຫ້ເຫັນການສວມໃສ່ເກີນຈຸດທີ່ແນ່ນອນຄວນໄດ້ຮັບການປ່ຽນແທນທັນທີ.
ຂະຫນາດແຜ່ນແລະຄວາມເຂົ້າກັນໄດ້ RPM:
ຂະໜາດທີ່ຖືກຕ້ອງ:ການນໍາໃຊ້ຂະຫນາດແຜ່ນທີ່ຖືກຕ້ອງສໍາລັບເຄື່ອງ grinder ແມ່ນສໍາຄັນ. ແຜ່ນດິສທີ່ມີຂະໜາດບໍ່ຖືກຕ້ອງອາດຈະໃສ່ບໍ່ສະໝ່ຳສະເໝີ ຫຼືມີຄວາມສ່ຽງດ້ານຄວາມປອດໄພ.
ຄວາມເຂົ້າກັນໄດ້ RPM:ການຍຶດຫມັ້ນກັບການປະຕິວັດທີ່ແນະນໍາຕໍ່ນາທີ (RPM) ສໍາລັບແຜ່ນ grinding ຮັບປະກັນການປະຕິບັດທີ່ດີທີ່ສຸດແລະປ້ອງກັນການສວມໃສ່ກ່ອນໄວອັນຄວນ.
ການບໍາລຸງຮັກສາເປັນປົກກະຕິ, ການຍຶດຫມັ້ນໃນເງື່ອນໄຂການດໍາເນີນງານທີ່ແນະນໍາ, ແລະການເລືອກແຜ່ນ grinding ທີ່ເຫມາະສົມສໍາລັບວຽກງານແມ່ນການປະຕິບັດທີ່ຈໍາເປັນເພື່ອຫຼຸດຜ່ອນການສວມໃສ່ແລະ tear. ໂດຍການເຂົ້າໃຈປັດໃຈທີ່ມີອິດທິພົນຕໍ່ການສວມໃສ່, ຜູ້ປະກອບການສາມາດເສີມຂະຫຍາຍຄວາມທົນທານແລະປະສິດທິພາບຂອງແຜ່ນ grinding, ປະກອບສ່ວນເຂົ້າໃນການປະຕິບັດການ grinding ທີ່ມີຄວາມປອດໄພແລະຜະລິດຕະພັນຫຼາຍກວ່າເກົ່າ.
ການຂັດທີ່ບໍ່ສະເຫມີກັນ
ການຂັດທີ່ບໍ່ສະ ໝໍ່າ ສະ ເໝີ ໝາຍ ເຖິງສະຖານະການທີ່ ໜ້າ ດິນບໍ່ບັນລຸຄວາມສອດຄ່ອງແລະກ້ຽງ. ບັນຫານີ້ສາມາດເກີດຂຶ້ນໄດ້ສໍາລັບເຫດຜົນຕ່າງໆແລະສາມາດສົ່ງຜົນກະທົບຕໍ່ຄຸນນະພາບຂອງ workpiece ໄດ້. ນີ້ແມ່ນປັດໃຈທົ່ວໄປທີ່ປະກອບສ່ວນເຂົ້າໃນການຂັດທີ່ບໍ່ສະເຫມີພາບແລະການແກ້ໄຂທີ່ເປັນໄປໄດ້:
ການເລືອກລໍ້ຂັດບໍ່ຖືກຕ້ອງ:
ການແກ້ໄຂ:ໃຫ້ແນ່ໃຈວ່າລໍ້ຂັດແມ່ນເຫມາະສົມສໍາລັບວັດສະດຸທີ່ເປັນດິນ. ວັດສະດຸທີ່ແຕກຕ່າງກັນຮຽກຮ້ອງໃຫ້ມີຄຸນສົມບັດຂັດສະເພາະ. ເລືອກປະເພດລໍ້ທີ່ເຫມາະສົມ, ຂະຫນາດຂອງ grit, ແລະພັນທະບັດສໍາລັບຄໍາຮ້ອງສະຫມັກ.
ການແຕ່ງຕົວລໍ້ທີ່ບໍ່ເໝາະສົມ:
ສາເຫດ:ລໍ້ຂັດທີ່ບໍ່ຖືກແຕ່ງຕົວຢ່າງຖືກຕ້ອງສາມາດເຮັດໃຫ້ເກີດການສວມໃສ່ທີ່ບໍ່ສະເຫມີກັນແລະການຕັດທີ່ບໍ່ມີປະສິດຕິຜົນ.
ການແກ້ໄຂ:ແຕ່ງຕົວລໍ້ຂັດຢ່າງເປັນປົກກະຕິເພື່ອຮັກສາຮູບຮ່າງຂອງມັນ ແລະເອົາສິ່ງເສດເຫຼືອທີ່ສະສົມອອກ. ການແຕ່ງຕົວທີ່ເຫມາະສົມຮັບປະກັນດ້ານການຕັດທີ່ສອດຄ່ອງ.
ນໍ້າອັດລົມ ຫຼືເຄື່ອງເຮັດຄວາມເຢັນບໍ່ພຽງພໍ:
ສາເຫດ:ການນໍາໃຊ້ບໍ່ພຽງພໍຫຼືບໍ່ຖືກຕ້ອງຂອງນ້ໍາ grinding ສາມາດສົ່ງຜົນໃຫ້ friction ແລະຄວາມຮ້ອນເພີ່ມຂຶ້ນ, ນໍາໄປສູ່ການ grinding uneven.
ການແກ້ໄຂ:ໃຊ້ນໍ້າອັດລົມ ຫຼືເຄື່ອງເຮັດຄວາມເຢັນທີ່ເໝາະສົມເພື່ອກະຈາຍຄວາມຮ້ອນ ແລະຫຼຸດຜ່ອນການສຽດສີ. ຄວາມເຢັນທີ່ເຫມາະສົມແມ່ນມີຄວາມຈໍາເປັນສໍາລັບການບັນລຸຜົນໄດ້ຮັບທີ່ເປັນເອກະພາບ.
ພາລາມິເຕີການຂັດທີ່ບໍ່ຖືກຕ້ອງ:
ສາເຫດ:ການນໍາໃຊ້ຕົວກໍານົດການການຕັດບໍ່ຖືກຕ້ອງເຊັ່ນ: ຄວາມໄວເກີນໄປ, ອັດຕາອາຫານ, ຫຼືຄວາມເລິກຂອງການຕັດສາມາດນໍາໄປສູ່ການບໍ່ສະເຫມີພາບ.
ການແກ້ໄຂ:ປັບຕົວກໍານົດການຂັດຕາມຄວາມຕ້ອງການວັດສະດຸແລະຄໍາຮ້ອງສະຫມັກ. ເບິ່ງຄໍາແນະນໍາຂອງຜູ້ຜະລິດສໍາລັບການຕັ້ງຄ່າທີ່ດີທີ່ສຸດ.
Won Grinding Wheel:
ສາເຫດ:ລໍ້ຂັດທີ່ສວມໃສ່ອາດຈະບໍ່ໃຫ້ພື້ນຜິວຕັດທີ່ສອດຄ່ອງ, ສົ່ງຜົນໃຫ້ມີການຂັດບໍ່ສະໝ່ຳສະເໝີ.
ການແກ້ໄຂ:ປ່ຽນລໍ້ຂັດເມື່ອມັນຮອດຈຸດສິ້ນສຸດຂອງຊີວິດທີ່ໃຊ້ໄດ້. ກວດກາລໍ້ເປັນປົກກະຕິສໍາລັບອາການຂອງການສວມໃສ່.
ຄວາມດັນ ຫຼື ອັດຕາອາຫານບໍ່ສະເໝີກັນ:
ສາເຫດ:ຄວາມກົດດັນທີ່ບໍ່ສອດຄ່ອງຫຼືອັດຕາອາຫານທີ່ບໍ່ສອດຄ່ອງໃນລະຫວ່າງການຂັດສາມາດນໍາໄປສູ່ການກໍາຈັດວັດສະດຸທີ່ບໍ່ສະຫມໍ່າສະເຫມີ.
ການແກ້ໄຂ:ນຳໃຊ້ຄວາມກົດດັນທີ່ເປັນເອກະພາບ ແລະຮັກສາອັດຕາອາຫານທີ່ສອດຄ່ອງກັນໃນທົ່ວແຜ່ນວຽກ. ທັກສະຂອງຜູ້ປະຕິບັດງານ ແລະຄວາມສົນໃຈໃນລາຍລະອຽດແມ່ນສໍາຄັນ.
ບັນຫາເຄື່ອງຈັກ:
ສາເຫດ:ບັນຫາທາງກົນຈັກກັບເຄື່ອງປີ້ງ, ເຊັ່ນ: ການຈັດລຽງຜິດ ຫຼືບັນຫາກັບແກນເຫຼັ້ມ, ສາມາດສົ່ງຜົນໃຫ້ການຂັດບໍ່ສະໝ່ຳສະເໝີ.
ການແກ້ໄຂ:ດໍາເນີນການກວດກາບໍາລຸງຮັກສາເປັນປົກກະຕິກ່ຽວກັບເຄື່ອງ grinding ໄດ້. ແກ້ໄຂບັນຫາກົນຈັກທັນທີເພື່ອຮັບປະກັນການເຮັດວຽກທີ່ເຫມາະສົມ.
ການສ້ອມແຊມ Workpiece:
ສາເຫດ:ຊິ້ນວຽກທີ່ຮັບປະກັນບໍ່ດີຫຼືບໍ່ຖືກຕ້ອງສາມາດນໍາໄປສູ່ການຂັດທີ່ບໍ່ສະເຫມີກັນ.
ການແກ້ໄຂ:ຮັບປະກັນການສ້ອມແຊມ ແລະ ການຈັດວາງຂອງວຽກຢ່າງຖືກຕ້ອງ. ຍຶດມັນໃຫ້ແຫນ້ນເພື່ອປ້ອງກັນການເຄື່ອນໄຫວໃນລະຫວ່າງການຂັດ.
ການແກ້ໄຂການຂັດທີ່ບໍ່ສະເຫມີກັນຮຽກຮ້ອງໃຫ້ມີການປະສົມປະສານຂອງການຕິດຕັ້ງອຸປະກອນທີ່ເຫມາະສົມ, ຕົວກໍານົດການປະຕິບັດງານທີ່ຖືກຕ້ອງ, ແລະການປະຕິບັດການບໍາລຸງຮັກສາເປັນປົກກະຕິ. ຜູ້ປະຕິບັດງານຄວນໄດ້ຮັບການຝຶກອົບຮົມເພື່ອກໍານົດແລະແກ້ໄຂບັນຫາທັນທີທັນໃດເພື່ອບັນລຸຜົນໄດ້ຮັບທີ່ມີຄຸນນະພາບສູງແລະສອດຄ່ອງໃນການນໍາໃຊ້ເຄື່ອງຂັດ. ການກວດກາເປັນປົກກະຕິແລະການຍຶດຫມັ້ນໃນການປະຕິບັດທີ່ດີທີ່ສຸດປະກອບສ່ວນເຂົ້າໃນການກໍາຈັດວັດສະດຸທີ່ມີປະສິດທິພາບແລະເປັນເອກະພາບໃນລະຫວ່າງຂະບວນການຂັດ.
ບັນຫາຄວາມຮ້ອນເກີນ
ການ overheating ໃນລະຫວ່າງການ grinding ເປັນບັນຫາທົ່ວໄປທີ່ສາມາດສົ່ງຜົນກະທົບຕໍ່ການປະຕິບັດຂອງທັງລໍ້ grinding ແລະ workpiece ໄດ້. ຄວາມຮ້ອນຫຼາຍເກີນໄປສາມາດນໍາໄປສູ່ບັນຫາຕ່າງໆ, ລວມທັງການຫຼຸດຜ່ອນອາຍຸຂອງລໍ້, ຄວາມເສຍຫາຍຄວາມຮ້ອນຕໍ່ກັບ workpiece, ແລະປະສິດທິພາບການ grinding ຫຼຸດລົງໂດຍລວມ. ນີ້ແມ່ນສາເຫດທີ່ເປັນໄປໄດ້ ແລະວິທີແກ້ໄຂສໍາລັບການແກ້ໄຂບັນຫາຄວາມຮ້ອນເກີນ:
ພາລາມິເຕີການຂັດທີ່ບໍ່ຖືກຕ້ອງ:
ສາເຫດ:ການນໍາໃຊ້ຕົວກໍານົດການ grinding ທີ່ບໍ່ຖືກຕ້ອງ, ເຊັ່ນຄວາມໄວຫຼາຍເກີນໄປ, ອັດຕາການໃຫ້ອາຫານ, ຫຼືຄວາມເລິກຂອງການຕັດ, ສາມາດສ້າງຄວາມຮ້ອນເກີນ.
ການແກ້ໄຂ:ປັບຕົວກໍານົດການຂັດພາຍໃນຂອບເຂດທີ່ແນະນໍາ. ປຶກສາຫາລືຄໍາແນະນໍາຂອງຜູ້ຜະລິດສໍາລັບການຕັ້ງຄ່າທີ່ດີທີ່ສຸດໂດຍອີງໃສ່ວັດສະດຸທີ່ເປັນພື້ນດິນ.
ການເຮັດຄວາມເຢັນ ຫຼືການຫຼໍ່ລື່ນບໍ່ພຽງພໍ:
ສາເຫດ:ການນໍາໃຊ້ບໍ່ພຽງພໍຂອງ coolant ຫຼືນ້ໍາ grinding ສາມາດເຮັດໃຫ້ເກີດ friction ແລະຄວາມຮ້ອນເພີ່ມຂຶ້ນ.
ການແກ້ໄຂ:ຮັບປະກັນການສະຫນອງທີ່ພຽງພໍຂອງ coolant ຫຼື lubricant ໃນລະຫວ່າງການຂະບວນການ grinding ໄດ້. ຄວາມເຢັນທີ່ເໝາະສົມຈະຊ່ວຍກະຈາຍຄວາມຮ້ອນ ແລະປ້ອງກັນຄວາມເສຍຫາຍຈາກຄວາມຮ້ອນ.
ການເລືອກລໍ້ບໍ່ຖືກຕ້ອງ:
ສາເຫດ:ການເລືອກລໍ້ຂັດທີ່ມີສະເພາະທີ່ບໍ່ເຫມາະສົມສໍາລັບອຸປະກອນການເປັນດິນສາມາດນໍາໄປສູ່ການ overheating ໄດ້.
ການແກ້ໄຂ:ເລືອກລໍ້ຂັດທີ່ມີປະເພດຂັດທີ່ຖືກຕ້ອງ, ຂະຫນາດຂອງເມັດ, ແລະພັນທະບັດສໍາລັບຄໍາຮ້ອງສະຫມັກສະເພາະ. ການຈັບຄູ່ລໍ້ກັບວັດສະດຸເຮັດໃຫ້ການຜະລິດຄວາມຮ້ອນຫຼຸດລົງ.
ບັນຫາວັດສະດຸ Workpiece:
ສາເຫດ:ວັດສະດຸບາງອັນ, ໂດຍສະເພາະແມ່ນເຄື່ອງໃຊ້ຄວາມຮ້ອນທີ່ບໍ່ດີ, ມັກຈະເກີດຄວາມຮ້ອນສູງເກີນໄປໃນລະຫວ່າງການຂັດ.
ການແກ້ໄຂ:ປັບຕົວກໍານົດການຂັດສໍາລັບວັດສະດຸທີ່ມີການນໍາຄວາມຮ້ອນຕ່ໍາ. ພິຈາລະນານໍາໃຊ້ລໍ້ຂັດພິເສດທີ່ອອກແບບມາສໍາລັບວັດສະດຸທີ່ອ່ອນໄຫວຕໍ່ຄວາມຮ້ອນ.
ບັນຫາການແຕ່ງຕົວລໍ້:
ສາເຫດ:ຄວາມບໍ່ສະຫມໍ່າສະເຫມີຫຼືການແຕ່ງຕົວທີ່ບໍ່ເຫມາະສົມຂອງລໍ້ຂັດສາມາດນໍາໄປສູ່ການຕິດຕໍ່ທີ່ບໍ່ສະເຫມີກັນແລະການສ້າງຄວາມຮ້ອນ.
ການແກ້ໄຂ:ແຕ່ງຕົວລໍ້ຂັດຢ່າງເປັນປົກກະຕິເພື່ອຮັກສາຮູບຮ່າງຂອງມັນ ແລະເອົາສິ່ງເສດເຫຼືອທີ່ຕິດຢູ່ກັບ glazing ອອກ. ລໍ້ແຕ່ງຕົວຢ່າງຖືກຕ້ອງຮັບປະກັນການປະຕິບັດການຂັດທີ່ສອດຄ່ອງ.
ການບໍາລຸງຮັກສາເຄື່ອງຈັກບໍ່ພຽງພໍ:
ສາເຫດ:ເຄື່ອງຈັກບົດທີ່ຮັກສາໄວ້ບໍ່ດີສາມາດເຮັດໃຫ້ເກີດບັນຫາຄວາມຮ້ອນເກີນ.
ການແກ້ໄຂ:ດໍາເນີນການບໍາລຸງຮັກສາເປັນປົກກະຕິກ່ຽວກັບເຄື່ອງ grinding, ລວມທັງການກວດສອບລະບົບ coolant, ກວດກາອຸປະກອນ dressing ລໍ້, ແລະຮັບປະກັນການສອດຄ່ອງທີ່ເຫມາະສົມ. ແກ້ໄຂບັນຫາກົນຈັກຢ່າງທັນການ.
ການໄຫຼຂອງຄວາມເຢັນລໍ້ບໍ່ພຽງພໍ:
ສາເຫດ:ການໄຫຼຂອງ coolant ທີ່ບໍ່ພຽງພໍກັບເຂດ grinding ສາມາດສົ່ງຜົນໃຫ້ການກະຈາຍຄວາມຮ້ອນຫຼຸດລົງ.
ການແກ້ໄຂ:ກວດເບິ່ງແລະປັບປຸງລະບົບການຈັດສົ່ງ coolant. ຮັບປະກັນວ່າເຄື່ອງເຮັດຄວາມເຢັນມີປະສິດຕິຜົນໄປຮອດເຂດການຂັດ ເພື່ອຮັກສາປະສິດທິພາບຄວາມເຢັນ.
ເວລາຂັດຫຼາຍເກີນໄປ:
ສາເຫດ:ໄລຍະເວລາການຂັດທີ່ຍາວນານໂດຍບໍ່ມີການພັກຜ່ອນສາມາດເຮັດໃຫ້ເກີດຄວາມຮ້ອນ.
ການແກ້ໄຂ:ປະຕິບັດການຂັດເປັນໄລຍະໆແລະອະນຸຍາດໃຫ້ພັກຜ່ອນເພື່ອປ້ອງກັນການສະສົມຄວາມຮ້ອນຫຼາຍເກີນໄປ. ວິທີການນີ້ແມ່ນມີຄວາມສໍາຄັນໂດຍສະເພາະສໍາລັບວຽກງານການຂັດຂະຫນາດໃຫຍ່ຫຼືທ້າທາຍ.
ການແກ້ໄຂບັນຫາຄວາມຮ້ອນເກີນໃນເຄື່ອງຂັດຮຽກຮ້ອງໃຫ້ມີວິທີການທີ່ສົມບູນແບບທີ່ກ່ຽວຂ້ອງກັບການຕິດຕັ້ງອຸປະກອນທີ່ເຫມາະສົມ, ຕົວກໍານົດການຂັດທີ່ເຫມາະສົມ, ແລະການປະຕິບັດການບໍາລຸງຮັກສາເປັນປົກກະຕິ. ຜູ້ປະຕິບັດການຄວນຕິດຕາມແລະຄວບຄຸມການຜະລິດຄວາມຮ້ອນໃນລະຫວ່າງຂະບວນການຂັດເພື່ອຮັບປະກັນການປະຕິບັດທີ່ດີທີ່ສຸດ, ອາຍຸຂອງເຄື່ອງມືທີ່ຍາວນານ, ແລະຜົນໄດ້ຮັບທີ່ມີຄຸນນະພາບສູງ.
ຄວາມກັງວົນກ່ຽວກັບການສັ່ນສະເທືອນ
ການສັ່ນສະເທືອນຫຼາຍເກີນໄປໃນລະຫວ່າງການປະຕິບັດງານເຄື່ອງປັ່ນສາມາດນໍາໄປສູ່ບັນຫາຕ່າງໆ, ລວມທັງການຫຼຸດຜ່ອນຄຸນນະພາບຂອງຫນ້າດິນ, ການສວມໃສ່ຂອງເຄື່ອງມືເພີ່ມຂຶ້ນ, ແລະຄວາມເສຍຫາຍທີ່ອາດເກີດຂື້ນກັບເຄື່ອງຂັດ. ການແກ້ໄຂຄວາມກັງວົນກ່ຽວກັບການສັ່ນສະເທືອນແມ່ນສໍາຄັນສໍາລັບການບັນລຸຂະບວນການຂັດທີ່ຊັດເຈນແລະປະສິດທິພາບ. ນີ້ແມ່ນສາເຫດທີ່ເປັນໄປໄດ້ ແລະວິທີແກ້ໄຂເພື່ອຫຼຸດຜ່ອນບັນຫາການສັ່ນສະເທືອນ:
ການສວມລໍ້ບໍ່ສະເຫມີກັນ:
ສາເຫດ:ການສວມໃສ່ທີ່ບໍ່ສະຫມໍ່າສະເຫມີຢູ່ໃນລໍ້ຂັດສາມາດສົ່ງຜົນໃຫ້ມີການຕິດຕໍ່ທີ່ບໍ່ສະເຫມີກັນກັບຊິ້ນວຽກ, ເຊິ່ງກໍ່ໃຫ້ເກີດການສັ່ນສະເທືອນ.
ການແກ້ໄຂ:ກວດກາ ແລະແຕ່ງຕົວລໍ້ຂັດເປັນປະຈຳເພື່ອຮັກສາພື້ນຜິວທີ່ສອດຄ່ອງ ແລະຮາບພຽງ. ການບໍາລຸງຮັກສາລໍ້ທີ່ຖືກຕ້ອງຊ່ວຍຫຼຸດຜ່ອນການສັ່ນສະເທືອນ.
ລໍ້ຂັດທີ່ບໍ່ສົມດຸນ:
ສາເຫດ:ຄວາມບໍ່ສົມດຸນໃນລໍ້ຂັດ, ບໍ່ວ່າຈະເປັນຍ້ອນການສວມໃສ່ທີ່ບໍ່ສະເຫມີກັນຫຼືຄວາມບົກຜ່ອງດ້ານການຜະລິດ, ສາມາດນໍາໄປສູ່ການສັ່ນສະເທືອນ.
ການແກ້ໄຂ:ດຸ່ນດ່ຽງລໍ້ຂັດໂດຍໃຊ້ເຄື່ອງດຸ່ນດ່ຽງລໍ້. ການດຸ່ນດ່ຽງຮັບປະກັນເຖິງແມ່ນວ່າການແຈກຢາຍນ້ໍາຫນັກແລະຫຼຸດຜ່ອນການສັ່ນສະເທືອນໃນລະຫວ່າງການປະຕິບັດງານ.
ການປັບທຽບເຄື່ອງບໍ່ພຽງພໍ:
ສາເຫດ:ການປັບທຽບທີ່ບໍ່ດີຫຼືການຈັດຕັ້ງຂອງເຄື່ອງປະກອບທີ່ບໍ່ຖືກຕ້ອງເຊັ່ນແກນລໍ້ ຫຼືໂຕະເຮັດວຽກສາມາດເຮັດໃຫ້ເກີດການສັ່ນສະເທືອນໄດ້.
ການແກ້ໄຂ:ປັບປັບແລະຈັດປະກອບຂອງເຄື່ອງຈັກເປັນປົກກະຕິເພື່ອຮັບປະກັນການທໍາງານທີ່ເຫມາະສົມ. ປະຕິບັດຕາມຄໍາແນະນໍາຂອງຜູ້ຜະລິດສໍາລັບການຕິດຕັ້ງແລະການຈັດຕໍາແຫນ່ງເຄື່ອງຈັກ.
ຄວາມບໍ່ສົມດຸນຂອງການເຮັດວຽກ:
ສາເຫດ:ຊິ້ນວຽກທີ່ບໍ່ສອດຄ່ອງຫຼືບໍ່ຖືກຮັບປະກັນສາມາດສ້າງຄວາມບໍ່ສົມດຸນແລະເຮັດໃຫ້ເກີດການສັ່ນສະເທືອນ.
ການແກ້ໄຂ:ຮັບປະກັນ workpiece ໄດ້ຢ່າງຖືກຕ້ອງ, ຮັບປະກັນວ່າມັນແມ່ນຕໍາແຫນ່ງເທົ່າທຽມກັນແລະ clamped. ແກ້ໄຂບັນຫາຄວາມບໍ່ສົມດຸນກ່ອນທີ່ຈະເລີ່ມຕົ້ນຂະບວນການຂັດ.
ການເລືອກລໍ້ບໍ່ຖືກຕ້ອງ:
ສາເຫດ:ການນໍາໃຊ້ລໍ້ທີ່ມີສະເພາະທີ່ບໍ່ເຫມາະສົມສາມາດເຮັດໃຫ້ເກີດການສັ່ນສະເທືອນໄດ້.
ການແກ້ໄຂ:ເລືອກລໍ້ຂັດທີ່ມີປະເພດຂັດທີ່ຖືກຕ້ອງ, ຂະຫນາດຂອງເມັດ, ແລະການຜູກມັດສໍາລັບວັດສະດຸທີ່ເປັນດິນ. ການຈັບຄູ່ລໍ້ກັບແອັບພລິເຄຊັນຊ່ວຍຫຼຸດຜ່ອນການສັ່ນສະເທືອນ.
ການສວມໃສ່ຂອງເຄື່ອງຈັກ:
ສາເຫດ:ອົງປະກອບຂອງເຄື່ອງຈັກທີ່ຂາດ ຫຼືເສຍຫາຍ, ເຊັ່ນລູກປືນ ຫຼື spindles, ສາມາດປະກອບສ່ວນກັບການສັ່ນສະເທືອນ.
ການແກ້ໄຂ:ກວດກາ ແລະປ່ຽນຊິ້ນສ່ວນເຄື່ອງທີ່ສວມໃສ່ເປັນປະຈຳ. ການບໍາລຸງຮັກສາທີ່ເຫມາະສົມຊ່ວຍປ້ອງກັນການສັ່ນສະເທືອນຫຼາຍເກີນໄປແລະຍືດອາຍຸຂອງເຄື່ອງຂັດ.
ການໄຫຼຂອງຄວາມເຢັນບໍ່ພຽງພໍ:
ສາເຫດ:ການໄຫຼຂອງ coolant ບໍ່ພຽງພໍກັບເຂດ grinding ສາມາດສົ່ງຜົນໃນການກໍ່ສ້າງຄວາມຮ້ອນແລະການສັ່ນສະເທືອນ.
ການແກ້ໄຂ:ເພີ່ມປະສິດທິພາບລະບົບການຈັດສົ່ງເຄື່ອງເຮັດຄວາມເຢັນເພື່ອຮັບປະກັນຄວາມເຢັນທີ່ເຫມາະສົມ. ຄວາມເຢັນທີ່ມີປະສິດທິພາບຊ່ວຍຫຼຸດຜ່ອນຄວາມສ່ຽງຕໍ່ການຂະຫຍາຍຄວາມຮ້ອນແລະການຫົດຕົວ, ເຊິ່ງສາມາດນໍາໄປສູ່ການສັ່ນສະເທືອນ.
ບັນຫາຜູ້ຖືເຄື່ອງມື:
ສາເຫດ:ບັນຫາກັບຕົວຍຶດເຄື່ອງມືຫຼືການໂຕ້ຕອບ spindle ສາມາດແນະນໍາການສັ່ນສະເທືອນ.
ການແກ້ໄຂ:ໃຫ້ແນ່ໃຈວ່າຕົວຍຶດເຄື່ອງມືຖືກຕິດຢູ່ຢ່າງປອດໄພແລະສອດຄ່ອງຢ່າງຖືກຕ້ອງກັບ spindle. ໃຊ້ຕົວຍຶດເຄື່ອງມືທີ່ມີຄຸນນະພາບສູງແລະຖືກຮັກສາຢ່າງຖືກຕ້ອງເພື່ອຫຼຸດຜ່ອນການສັ່ນສະເທືອນ.
ມູນນິທິເຄື່ອງຈັກ:
ສາເຫດ:ພື້ນຖານເຄື່ອງຈັກທີ່ບໍ່ດີຫຼືການສະຫນັບສະຫນູນບໍ່ພຽງພໍສາມາດຂະຫຍາຍການສັ່ນສະເທືອນ.
ການແກ້ໄຂ:ໃຫ້ແນ່ໃຈວ່າເຄື່ອງຂັດໄດ້ຖືກຕິດຕັ້ງຢູ່ໃນພື້ນຖານທີ່ຫມັ້ນຄົງແລະຖືກອອກແບບຢ່າງຖືກຕ້ອງ. ແກ້ໄຂບັນຫາໂຄງສ້າງຕ່າງໆເພື່ອຫຼຸດຜ່ອນການສັ່ນສະເທືອນທີ່ສົ່ງໄປຫາເຄື່ອງຈັກ.
ການແກ້ໄຂບັນຫາການສັ່ນສະເທືອນຢ່າງມີປະສິດທິພາບໃນການຂັດຮຽກຮ້ອງໃຫ້ມີການປະສົມປະສານຂອງການບໍາລຸງຮັກສາເຄື່ອງຈັກທີ່ເຫມາະສົມ, ການຄັດເລືອກລໍ້, ແລະການຈັດການຊິ້ນວຽກ. ຜູ້ປະຕິບັດງານຄວນປະຕິບັດການກວດກາແລະບໍາລຸງຮັກສາເປັນປົກກະຕິເພື່ອກໍານົດແລະແກ້ໄຂບັນຫາທັນທີ, ສົ່ງຜົນໃຫ້ມີການປັບປຸງປະສິດທິພາບແລະຄຸນນະພາບ.
ການໂຫຼດບັນຫາໃນການຂັດ
Loading in grinding ຫມາຍເຖິງປະກົດການທີ່ຊ່ອງຫວ່າງລະຫວ່າງເມັດພືດຂັດໃນລໍ້ grinding ໄດ້ເຕັມໄປດ້ວຍວັດສະດຸເປັນດິນ, ສົ່ງຜົນໃຫ້ການປະຕິບັດການຕັດຫຼຸດລົງແລະ friction ເພີ່ມຂຶ້ນ. ການໂຫຼດສາມາດສົ່ງຜົນກະທົບທາງລົບຕໍ່ປະສິດທິພາບແລະຄຸນນະພາບຂອງຂະບວນການຂັດ. ນີ້ແມ່ນສາເຫດທີ່ເປັນໄປໄດ້ ແລະວິທີແກ້ໄຂເພື່ອແກ້ໄຂບັນຫາການໂຫຼດ:
ວັດສະດຸ Workpiece ອ່ອນ:
ສາເຫດ:ການຂັດວັດສະດຸອ່ອນໆສາມາດນໍາໄປສູ່ການອຸດຕັນຢ່າງໄວວາຂອງເມັດພືດທີ່ຂັດ.
ການແກ້ໄຂ:ໃຊ້ລໍ້ຂັດທີ່ມີໂຄງສ້າງທີ່ອ່ອນກວ່າ ແລະເປີດເມື່ອເຮັດວຽກກັບວັດສະດຸທີ່ອ່ອນກວ່າ. ນີ້ຊ່ວຍປ້ອງກັນການໂຫຼດໄວແລະອະນຸຍາດໃຫ້ກໍາຈັດຊິບທີ່ມີປະສິດທິພາບ.
ການປົນເປື້ອນວັດສະດຸ:
ສາເຫດ:ສິ່ງປົນເປື້ອນທີ່ມີຢູ່ໃນອຸປະກອນການເຮັດວຽກ, ເຊັ່ນນໍ້າມັນ, ນໍ້າມັນ, ຫຼືສານຕົກຄ້າງຂອງເຄື່ອງເຮັດຄວາມເຢັນ, ສາມາດປະກອບສ່ວນເຂົ້າໃນການໂຫຼດໄດ້.
ການແກ້ໄຂ:ຮັບປະກັນການທໍາຄວາມສະອາດທີ່ເຫມາະສົມຂອງ workpiece ກ່ອນທີ່ຈະ grinding ເພື່ອເອົາສິ່ງປົນເປື້ອນ. ໃຊ້ນ້ໍາຕັດທີ່ເຫມາະສົມຫຼື coolant ເພື່ອຫຼຸດຜ່ອນການໂຫຼດ.
ຄໍາຮ້ອງສະຫມັກ Coolant ບໍ່ຖືກຕ້ອງ:
ສາເຫດ:ການນຳໃຊ້ເຄື່ອງເຮັດຄວາມເຢັນບໍ່ພຽງພໍ ຫຼື ບໍ່ຖືກຕ້ອງສາມາດນຳໄປສູ່ການຫຼໍ່ລື່ນ ແລະ ຄວາມເຢັນບໍ່ພຽງພໍ, ເຮັດໃຫ້ເກີດການໂຫຼດໄດ້.
ການແກ້ໄຂ:ເພີ່ມປະສິດທິພາບການໄຫຼຂອງ coolant ແລະຄວາມເຂັ້ມຂົ້ນ. ໃຫ້ແນ່ໃຈວ່າເຄື່ອງເຮັດຄວາມເຢັນມີປະສິດຕິຜົນໄປຮອດເຂດການຂັດເພື່ອຫລໍ່ລື່ນແລະເຢັນຂະບວນການ, ປ້ອງກັນການໂຫຼດ.
ຄວາມຄົມຊັດຂອງລໍ້ບໍ່ພຽງພໍ:
ສາເຫດ:ລໍ້ຂັດທີ່ຈືດໆ ຫຼືສວມໃສ່ແມ່ນມີຄວາມສ່ຽງຕໍ່ການໂຫຼດຫຼາຍຂຶ້ນຍ້ອນວ່າພວກມັນສູນເສຍປະສິດທິພາບການຕັດ.
ການແກ້ໄຂ:ແຕ່ງຕົວເປັນປະຈຳ ແລະ ໝຸນເຄື່ອງປີ້ງ ເພື່ອຮັກສາຄວາມຄົມຊັດ. ໃຊ້ເຄື່ອງແຕ່ງກາຍລໍ້ເພື່ອເປີດເຜີຍເມັດພືດທີ່ມີສານຂັດສົດ ແລະເສີມຂະຫຍາຍການປະຕິບັດການຕັດ.
ຄວາມໄວລໍ້ຕໍ່າ:
ສາເຫດ:ການປະຕິບັດການຂອງລໍ້ຂະຫນາດນ້ອຍຢູ່ໃນຄວາມໄວຕ່ໍາອາດຈະບໍ່ໄດ້ໃຫ້ຜົນບັງຄັບໃຊ້ centrifugal ພຽງພໍທີ່ຈະຂັບໄລ່ chip, ເຮັດໃຫ້ການໂຫຼດ.
ການແກ້ໄຂ:ໃຫ້ແນ່ໃຈວ່າເຄື່ອງຂັດເຮັດວຽກຢູ່ໃນຄວາມໄວທີ່ແນະນໍາສໍາລັບການປະສົມລໍ້ແລະຊິ້ນວຽກສະເພາະ. ຄວາມໄວທີ່ສູງຂຶ້ນສາມາດຊ່ວຍໃນການກໍາຈັດຊິບທີ່ດີກວ່າ.
ຄວາມກົດດັນຫຼາຍເກີນໄປ:
ສາເຫດ:ການໃຊ້ຄວາມກົດດັນຫຼາຍເກີນໄປໃນລະຫວ່າງການຂັດສາມາດບັງຄັບວັດສະດຸເຂົ້າໄປໃນລໍ້, ເຊິ່ງກໍ່ໃຫ້ເກີດການໂຫຼດ.
ການແກ້ໄຂ:ໃຊ້ຄວາມກົດດັນປານກາງແລະສອດຄ່ອງ. ປັບອັດຕາອາຫານເພື່ອໃຫ້ລໍ້ຕັດຢ່າງມີປະສິດທິພາບໂດຍບໍ່ມີຄວາມກົດດັນຫຼາຍເກີນໄປທີ່ນໍາໄປສູ່ການໂຫຼດ.
ຂໍ້ມູນຈໍາເພາະຂອງລໍ້ຜິດ:
ສາເຫດ:ການນໍາໃຊ້ລໍ້ຂັດທີ່ມີຂໍ້ກໍານົດທີ່ບໍ່ຖືກຕ້ອງສໍາລັບການອຸປະກອນການເປັນດິນສາມາດເຮັດໃຫ້ເກີດການໂຫຼດໄດ້.
ການແກ້ໄຂ:ເລືອກລໍ້ຂັດທີ່ມີປະເພດຂັດທີ່ເຫມາະສົມ, ຂະຫນາດ grit, ແລະພັນທະບັດສໍາລັບຄໍາຮ້ອງສະຫມັກສະເພາະ. ການຈັບຄູ່ລໍ້ກັບວັດສະດຸຊ່ວຍປ້ອງກັນການໂຫຼດ.
ການທຳຄວາມສະອາດນ້ຳເຢັນບໍ່ພຽງພໍ:
ສາເຫດ:ການປົນເປື້ອນຫຼື coolant ເກົ່າອາດຈະປະກອບສ່ວນກັບບັນຫາການໂຫຼດ.
ການແກ້ໄຂ:ເຮັດຄວາມສະອາດຢ່າງເປັນປົກກະຕິແລະປ່ຽນເຄື່ອງເຮັດຄວາມເຢັນເພື່ອປ້ອງກັນການສ້າງສິ່ງປົນເປື້ອນ. coolant ສົດແລະສະອາດເສີມຂະຫຍາຍການ lubrication ແລະຄວາມເຢັນ, ຫຼຸດຜ່ອນຄວາມເປັນໄປໄດ້ຂອງການໂຫຼດ.
ເຕັກນິກການແຕ່ງຕົວທີ່ບໍ່ເຫມາະສົມ:
ສາເຫດ:ການແຕ່ງຕົວທີ່ບໍ່ຖືກຕ້ອງຂອງລໍ້ຂັດສາມາດນໍາໄປສູ່ຄວາມຜິດປົກກະຕິແລະການໂຫຼດ.
ການແກ້ໄຂ:ແຕ່ງຕົວລໍ້ໃຫ້ຖືກຕ້ອງໂດຍໃຊ້ເຄື່ອງມືແຕ່ງຕົວທີ່ເຫມາະສົມ. ໃຫ້ແນ່ໃຈວ່າ profile ລໍ້ແມ່ນສອດຄ່ອງແລະບໍ່ມີສະຫມໍ່າສະເຫມີເພື່ອປ້ອງກັນການໂຫຼດ.
ການແກ້ໄຂບັນຫາການໂຫຼດຢ່າງມີປະສິດທິພາບປະກອບດ້ວຍການລວມກັນຂອງການເລືອກລໍ້ທີ່ເຫມາະສົມ, ການຕິດຕັ້ງເຄື່ອງຈັກ, ແລະການປະຕິບັດການບໍາລຸງຮັກສາ. ຜູ້ປະຕິບັດການຄວນປະຕິບັດຕາມຂັ້ນຕອນທີ່ແນະນໍາ, ໃຊ້ຕົວກໍານົດການຂັດທີ່ເຫມາະສົມ, ແລະປະຕິບັດການແຕ່ງຕົວລໍ້ປົກກະຕິເພື່ອຫຼຸດຜ່ອນການໂຫຼດແລະເພີ່ມປະສິດທິພາບການຂັດ.
ການເລືອກແຜ່ນທີ່ຖືກຕ້ອງແມ່ນມີຄວາມສໍາຄັນສໍາລັບການບັນລຸຜົນໄດ້ຮັບທີ່ດີທີ່ສຸດໃນການນໍາໃຊ້ການເຮັດວຽກໂລຫະແລະການຜະລິດຕ່າງໆ. ການຄັດເລືອກແມ່ນຂຶ້ນກັບປັດໃຈເຊັ່ນ: ວັດສະດຸທີ່ກໍາລັງເຮັດວຽກ, ສໍາເລັດຮູບທີ່ຕ້ອງການ, ແລະປະເພດຂອງເຄື່ອງ grinder ທີ່ຖືກນໍາໃຊ້.
ການເລືອກແຜ່ນຕັດທີ່ເຫມາະສົມ
ຄວາມເຂົ້າກັນໄດ້ຂອງວັດສະດຸ:
ໂລຫະ ferous (ເຫຼັກກ້າ, ເຫຼັກ):ໃຊ້ແຜ່ນບົດທີ່ອອກແບບໂດຍສະເພາະສໍາລັບໂລຫະ ferrous. ແຜ່ນເຫຼົ່ານີ້ມັກຈະມີສານຂັດທີ່ເຫມາະສົມສໍາລັບຄວາມແຂງຂອງເຫລໍກແລະມີຄວາມສ່ຽງຕໍ່ການໂຫຼດຫນ້ອຍ.
ໂລຫະທີ່ບໍ່ແມ່ນເຫຼັກ (ອາລູມີນຽມ, ທອງເຫຼືອງ):ເລືອກແຜ່ນທີ່ມີສານຂັດທີ່ເຫມາະສົມສໍາລັບໂລຫະທີ່ອ່ອນກວ່າເພື່ອປ້ອງກັນການອຸດຕັນ. ແຜ່ນອາລູມິນຽມ oxide ຫຼືຊິລິໂຄນຄາໄບເປັນທາງເລືອກທົ່ວໄປ.
ວັດສະດຸຂັດ:
ອະລູມິນຽມອອກໄຊ:ເຫມາະສໍາລັບການນໍາໃຊ້ທົ່ວໄປໃນການຂັດໂລຫະ ferrous. ມັນທົນທານແລະຫລາກຫລາຍ.
Zirconia Alumina:ສະຫນອງປະສິດທິພາບການຕັດທີ່ສູງຂຶ້ນແລະອາຍຸຍືນ, ເຮັດໃຫ້ມັນເຫມາະສົມສໍາລັບການຂັດຮຸກຮານກ່ຽວກັບໂລຫະ ferrous ແລະທີ່ບໍ່ແມ່ນ ferrous.
Silicon Carbide:ເຫມາະສໍາລັບການຂັດໂລຫະທີ່ບໍ່ແມ່ນເຫຼັກແລະແກນ. ມັນແຫຼມກວ່າແຕ່ທົນທານຫນ້ອຍກວ່າອາລູມິນຽມອອກໄຊ.
ຂະຫນາດ Grit:
ຫຍາບຄາຍ (24-36):ການກໍາຈັດຫຼັກຊັບຢ່າງໄວວາແລະການຂັດຫນ້າທີ່ຫນັກແຫນ້ນ.
ຂະຫນາດກາງ Grit (40-60):ດຸ່ນດ່ຽງການກໍາຈັດຫຼັກຊັບແລະການສໍາເລັດຮູບດ້ານ.
ເມັດລະອຽດ (80-120):ສະຫນອງການສໍາເລັດຮູບກ້ຽງ, ເຫມາະສົມສໍາລັບການກະກຽມດ້ານແລະການຂັດແສງສະຫວ່າງ.
ປະເພດລໍ້:
ປະເພດ 27 (ສູນຊຶມເສົ້າ):ແຜ່ນມາດຕະຖານເຊັ່ນແຜ່ນທີ່ມີພື້ນຜິວຮາບພຽງ, ເຫມາະສໍາລັບການຂັດຫນ້າດິນແລະວຽກຂອບ.
ປະເພດ 29 (ຮູບຈວຍ):ການອອກແບບມຸມສໍາລັບການກໍາຈັດຫຼັກຊັບຮຸກຮານແລະການຜະສົມພື້ນຜິວທີ່ດີກວ່າ.
ປະເພດ 1 (ກົງ):ໃຊ້ສໍາລັບຄໍາຮ້ອງສະຫມັກຕັດ. ມັນສະຫນອງ profile ບາງໆສໍາລັບການຕັດທີ່ຖືກຕ້ອງ.
ຄໍາຮ້ອງສະຫມັກ:
ການຂັດ:ແຜ່ນບົດມາດຕະຖານສໍາລັບການໂຍກຍ້າຍວັດສະດຸແລະຮູບຮ່າງ.
ການຕັດ:ໃຊ້ລໍ້ຕັດສໍາລັບການຕັດຜ່ານໂລຫະ, ສະຫນອງແຂບຊື່ແລະສະອາດ.
ແຜ່ນ Flap:ສົມທົບການ grinding ແລະສໍາເລັດຮູບໃນຫນຶ່ງ. ເຫມາະສໍາລັບການຜະສົມຜະສານແລະກ້ຽງ.
ຄວາມເຂົ້າກັນໄດ້ກັບ Grinder:
ໃຫ້ແນ່ໃຈວ່າແຜ່ນເຄື່ອງຂັດແມ່ນເຂົ້າກັນໄດ້ກັບປະເພດແລະຄວາມໄວຂອງເຄື່ອງ grinder ທີ່ຖືກນໍາໃຊ້. ກວດເບິ່ງຄໍາແນະນໍາຂອງຜູ້ຜະລິດສໍາລັບ RPM ສູງສຸດ (ການປະຕິວັດຕໍ່ນາທີ) ຂອງແຜ່ນ.
ສະເພາະໜ້າວຽກ:
ການກໍາຈັດຫຼັກຊັບຫນັກ:ເລືອກແຜ່ນຫຍາບແລະແຜ່ນປະເພດ 27 ຫຼືປະເພດ 29 ສໍາລັບການກໍາຈັດວັດສະດຸທີ່ມີປະສິດທິພາບ.
ການສໍາເລັດຮູບຫນ້າດິນ:ເລືອກເອົາ grits ຂະຫນາດກາງຫາລະອຽດທີ່ມີແຜ່ນ flap ສໍາລັບການສໍາເລັດຮູບກ້ຽງ.
ການພິຈາລະນາຄວາມປອດໄພ:
ປະຕິບັດຕາມຄໍາແນະນໍາດ້ານຄວາມປອດໄພ, ລວມທັງການໃສ່ອຸປະກອນປ້ອງກັນສ່ວນບຸກຄົນທີ່ເຫມາະສົມ (PPE) ເຊັ່ນ: ແວ່ນຕາຄວາມປອດໄພແລະຖົງມື.
ເລືອກແຜ່ນເສີມເພື່ອຄວາມທົນທານ ແລະຄວາມປອດໄພ.
ຍີ່ຫໍ້ແລະຄຸນນະພາບ:
ເລືອກແຜ່ນຈາກຍີ່ຫໍ້ທີ່ມີຊື່ສຽງທີ່ມີຊື່ສຽງສໍາລັບຄຸນນະພາບແລະຄວາມສອດຄ່ອງ. ແຜ່ນຄຸນນະພາບສູງໃຫ້ປະສິດທິພາບທີ່ດີຂຶ້ນ ແລະທົນທານ.
ການພິຈາລະນາຄ່າໃຊ້ຈ່າຍ:
ດຸ່ນດ່ຽງຄ່າໃຊ້ຈ່າຍເບື້ອງຕົ້ນກັບອາຍຸການຄາດການແລະປະສິດທິພາບຂອງແຜ່ນ grinding. ແຜ່ນຄຸນນະພາບສູງອາດຈະມີຕົ້ນທຶນສູງກວ່າແຕ່ສາມາດໃຫ້ມູນຄ່າທີ່ດີກວ່າໃນໄລຍະເວລາ.
ໂດຍການພິຈາລະນາປັດໃຈເຫຼົ່ານີ້, ຜູ້ປະກອບການສາມາດເລືອກແຜ່ນ grinding ທີ່ເຫມາະສົມສໍາລັບຄໍາຮ້ອງສະຫມັກສະເພາະຂອງເຂົາເຈົ້າ, ຮັບປະກັນປະສິດທິພາບ, ຄວາມປອດໄພ, ແລະຜົນໄດ້ຮັບທີ່ດີທີ່ສຸດ.
ສະຫຼຸບ
ສະຫລຸບລວມແລ້ວ, ການເລືອກແຜ່ນບົດທີ່ເໝາະສົມແມ່ນເປັນລັກສະນະສຳຄັນຂອງການບັນລຸຜົນການງານໂລຫະ ແລະ ການຜະລິດສຳເລັດຮູບ. ທາງເລືອກແມ່ນຂຶ້ນກັບປັດໃຈຕ່າງໆເຊັ່ນວັດສະດຸທີ່ກໍາລັງເຮັດວຽກ, ສໍາເລັດຮູບທີ່ຕ້ອງການ, ແລະປະເພດຂອງເຄື່ອງປັ່ນ. ໂດຍການພິຈາລະນາຄວາມເຂົ້າກັນໄດ້ຂອງວັດສະດຸ, ປະເພດຂັດ, ຂະຫນາດຂອງແຜ່ນ, ປະເພດລໍ້, ຄໍາຮ້ອງສະຫມັກ, ຄວາມເຂົ້າກັນໄດ້ຂອງເຄື່ອງ grinder, ສະເພາະຂອງວຽກງານ, ຄວາມປອດໄພ, ຄຸນນະພາບຍີ່ຫໍ້, ແລະຄ່າໃຊ້ຈ່າຍ, ຜູ້ປະກອບການສາມາດຕັດສິນໃຈຢ່າງຈະແຈ້ງເພື່ອເພີ່ມປະສິດທິພາບແລະຄວາມປອດໄພໃນຂະບວນການຂັດຂອງພວກເຂົາ.
ມັນເປັນສິ່ງຈໍາເປັນທີ່ຈະຕ້ອງປະຕິບັດຕາມຄໍາແນະນໍາດ້ານຄວາມປອດໄພ, ໃສ່ອຸປະກອນປ້ອງກັນສ່ວນບຸກຄົນທີ່ເຫມາະສົມ, ແລະປະຕິບັດຕາມຄໍາແນະນໍາຂອງຜູ້ຜະລິດສໍາລັບການເຂົ້າກັນໄດ້ຂອງເຄື່ອງ grinder ແລະແຜ່ນ. ບໍ່ວ່າຈະເປັນສໍາລັບການໂຍກຍ້າຍຫຼັກຊັບຫນັກ, ສໍາເລັດຮູບດ້ານ, ຫຼືຄໍາຮ້ອງສະຫມັກການຕັດ, ແຜ່ນ grinding ທີ່ຖືກຕ້ອງສາມາດສົ່ງຜົນກະທົບຕໍ່ຄຸນນະພາບແລະປະສິດທິພາບຂອງການເຮັດວຽກຢ່າງຫຼວງຫຼາຍ.
ນອກຈາກນັ້ນ, ການກວດສອບການສວມໃສ່ເປັນໄລຍະໆ, ແກ້ໄຂບັນຫາຕ່າງໆເຊັ່ນ: ຄວາມຮ້ອນເກີນໄປແລະການສັ່ນສະເທືອນ, ແລະການເຂົ້າໃຈບັນຫາການໂຫຼດໄດ້ປະກອບສ່ວນເຂົ້າໃນການຍືດອາຍຸຂອງແຜ່ນຂັດແລະຮັບປະກັນການປະຕິບັດທີ່ສອດຄ່ອງ.
ສະຫລຸບລວມແລ້ວ, ວິທີການທີ່ມີຂໍ້ມູນດີ ແລະເປັນລະບົບໃນການເລືອກ, ນຳໃຊ້, ແລະ ການຮັກສາແຜ່ນຂັດແມ່ນກຸນແຈສຳຄັນໃນການບັນລຸຜົນທີ່ດີທີ່ສຸດ, ເສີມຂະຫຍາຍຜົນຜະລິດ, ແລະ ຮັບປະກັນສະພາບແວດລ້ອມການເຮັດວຽກທີ່ປອດໄພ.
ເວລາປະກາດ: ມັງກອນ-12-2024